Stock Management Solutions You Can Trust
Efficient and reliable fleet installation hinges on dependable stock management, a core focus at Nationwide Fleet Installations.
Trusted by Fleet Managers & Vehicle Technology Suppliers Across The UK
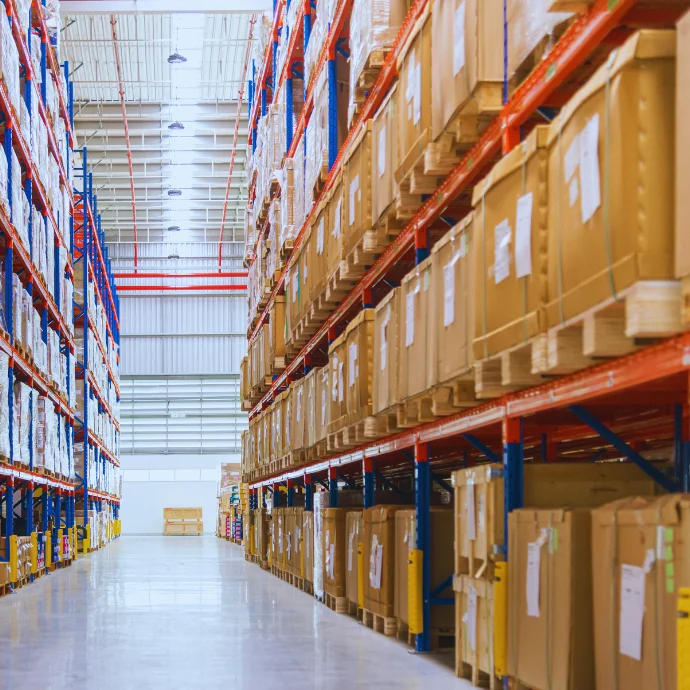
stock management
When it comes to arranging fleet installation solutions for our clients across the UK, stock management is key. The efficient control of vehicle technology plays a crucial part in the success of every fleet installation project we take on. Over the years we have been in business, we have learnt that it is far better to have a plan in place to manage the equipment stock for our clients than to rush ahead with the project and hope for the best.
What Nationwide Fleet Installations Can Do For You
We have on-site and off-site storage facilities that provide us with around 5000 sq ft of storage space. Not only does this give us all the room we need to hold significant amounts of stock, but it also allows us to handle fluctuations in our stock holdings. This is what you can expect from us:
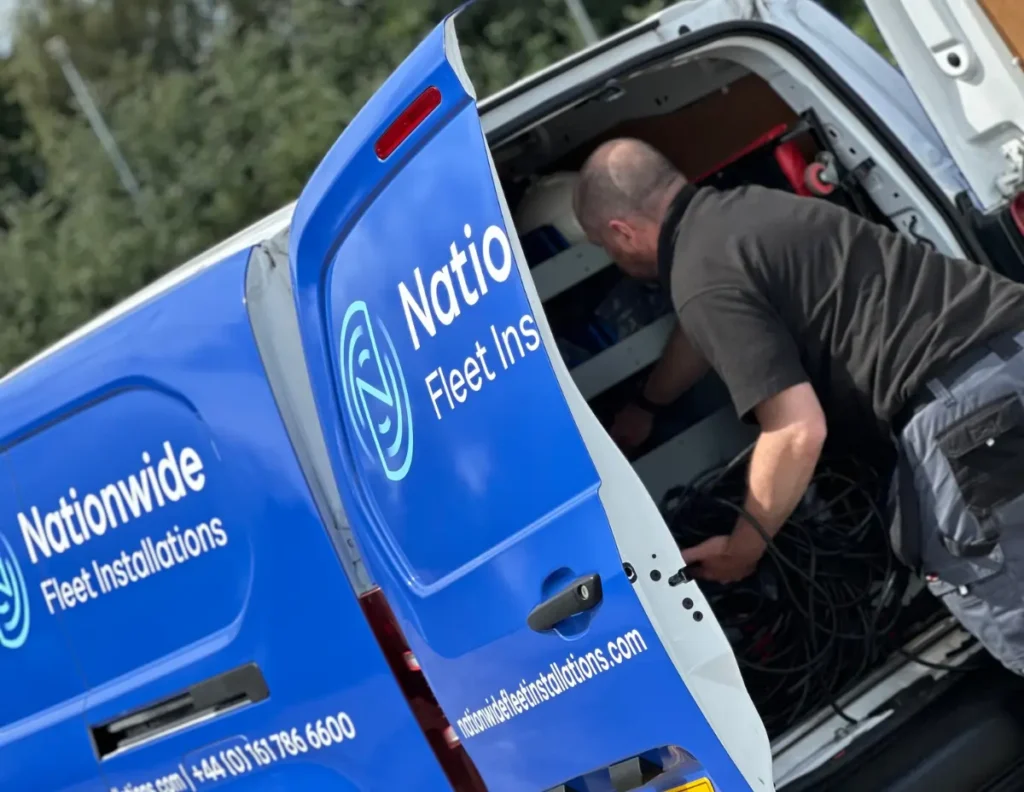
Basic Stock Handling
Our basic stock management service involves receiving equipment from our customers, recording the stock, and storing the items until they are needed. When they are ready to be installed, we record the time and location of dispatch, followed by the installation details once the job is completed.
Complex Stock Handling
In addition to our basic stock handling solutions, we also deal with more complex shipments. These typically include dispatching spare parts for a service job, receiving and recording returned equipment and faulty components, and recording details of any repair work undertaken by our engineers.
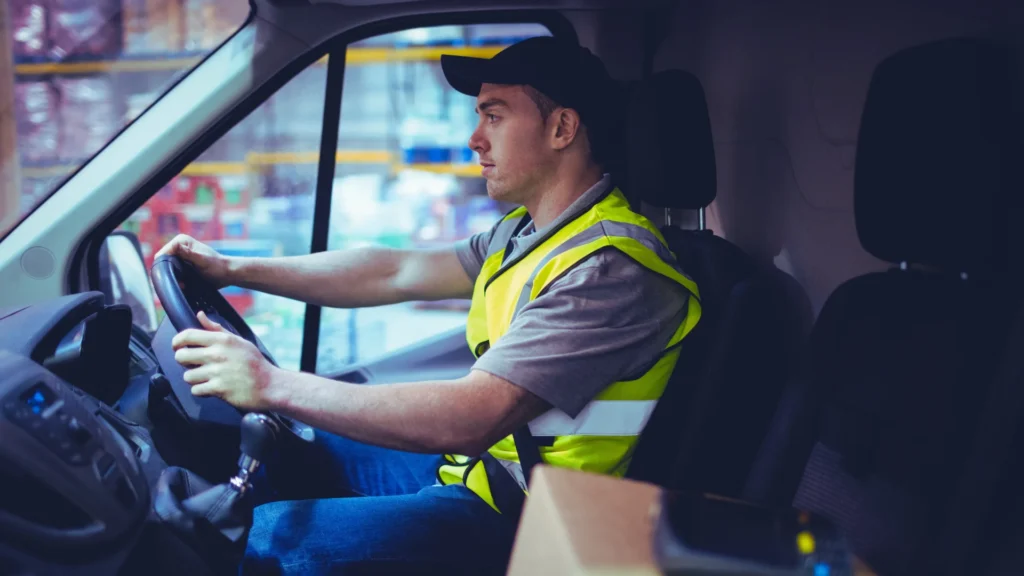
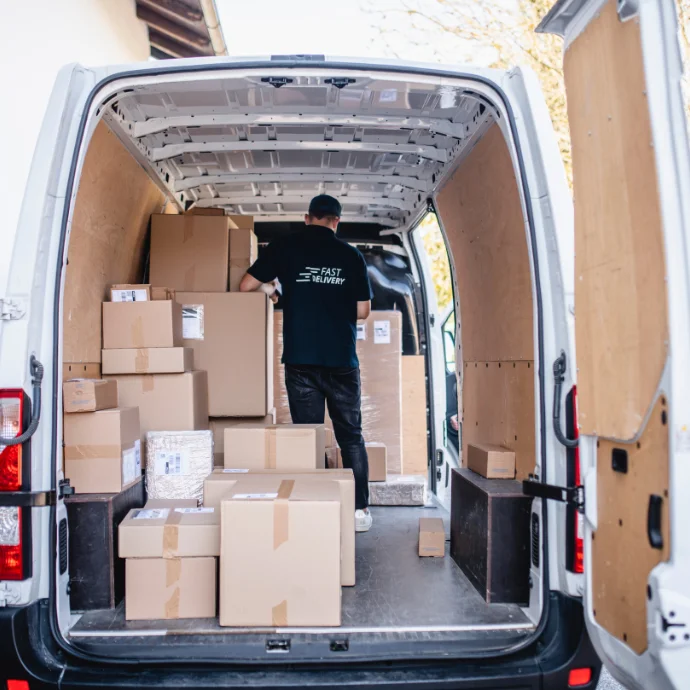
Stock Control
Sometimes our customers overestimate the size of their fleet, and some of the equipment that we dispatch ends up not being used. Without our rigorous stock control policies in place, this equipment can be lost, causing repercussions for our customers and ourselves. The time and care we take to record every stock item’s journey from receipt to installation or return is the reason we are a fleet installation firm you can trust.
International warehousing and dispatch
We manage significant levels of stock for several of our customers, often including more than 200 different stock items. If you are an international supplier, we can receive and fulfil stock orders from our main storage facility in Manchester, wherever you’re based.
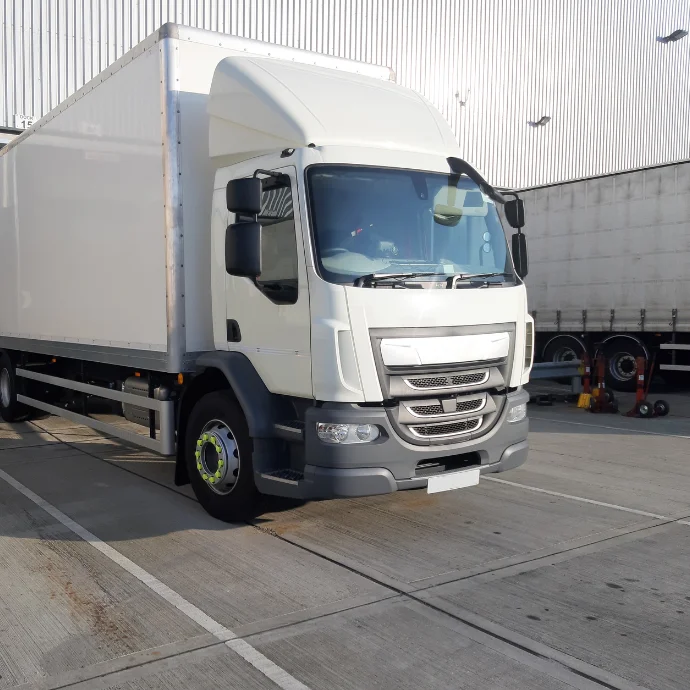
A Multi-person Stores Team
Once the above factors have been resolved, we can develop a suitable telematics and vehicle technology project rollout plan and allocate our engineering resources accordingly. At this phase of the operation, the project is handed over to the Project Support Team, which deals with administration and planning as well as the physical handling of stock.
Stock Management With An Easy Plan
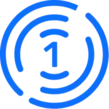
Get In Touch
Get in touch with us with your stock quantities, locations and when you need it dispatched for installation
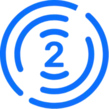
Confirm Your Booking
We will create a custom project plan with minimal disruption to your operations.
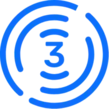
Installation day
We will schedule installation with your nominated contact without your further input.
Get In Touch
For stock management solutions you can depend upon across the UK, contact Nationwide Fleet Installations today.
Call us on 0161 786 6600 or email the team at info@nationwidefleetinstallations.com, and one of our team members will get back to you.