Project Management Solutions You Can Trust
Comprehensive solutions that go beyond installation ready to assist you at every stage of your vehicle technology’s life cycle, including installation, servicing, maintenance, and defleeting.
Trusted by Fleet Managers & Vehicle Technology Suppliers Across The UK
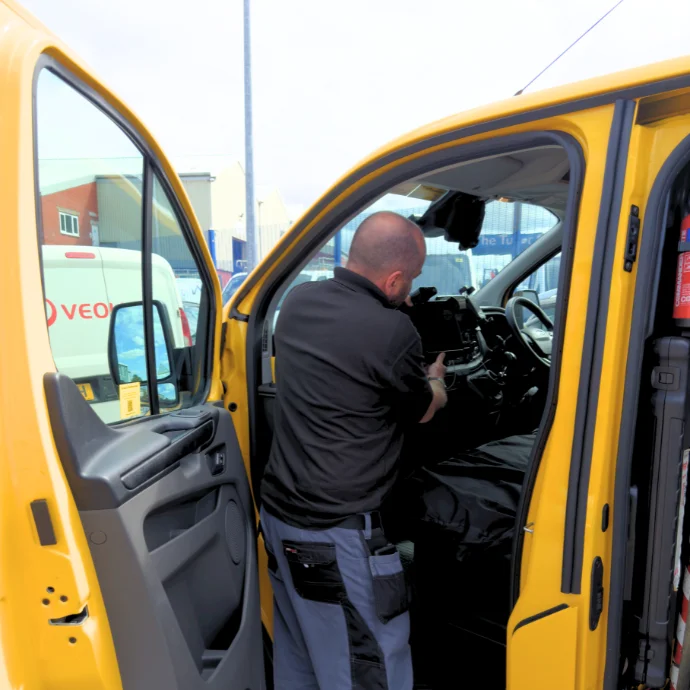
For Every Type Of Installation
Here at Nationwide Fleet Installations, we deal with installation projects of varying sizes and complexity.
In order to provide the first-class service that has become our trademark, every job we take on is assigned its own dedicated Project Manager, together with a Project Support Team to assist with the logistics and administration of the job in question.
The Project Management Process
We have been part of the fleet installation industry for more than 25 years, and in that time, we have developed and honed our project management process to ensure an efficient and orderly rollout of vehicle technology installations.
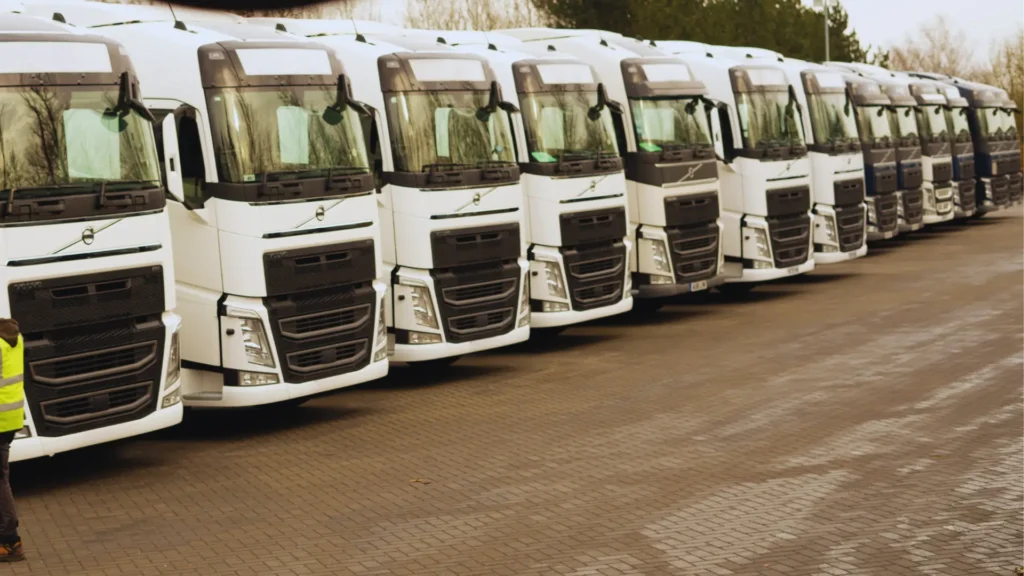
All Size Of Fleets
We have worked on all sizes of fleets, from a few hundred vehicles to more than 30,000 in a single project. Thanks to the proven project management methods we employ, every job is completed within the agreed timescales and to the high standards expected by our valued customers.
A Dedicated Project Manager and Support Team
Each of our project managers is an experienced member of staff with considerable expertise in the fleet installation industry. They will have a track record of working on other projects of a similar scale and complexity, giving you the assurance you need to know that your project will be a success.
Their Project Support Team is composed of members of our administration team. These experienced members of staff are experts in recording, logging, and cross-referencing information, ensuring that all pieces of vehicle technology are monitored throughout the lifespan of the project, from initial receipt to final installation and testing.
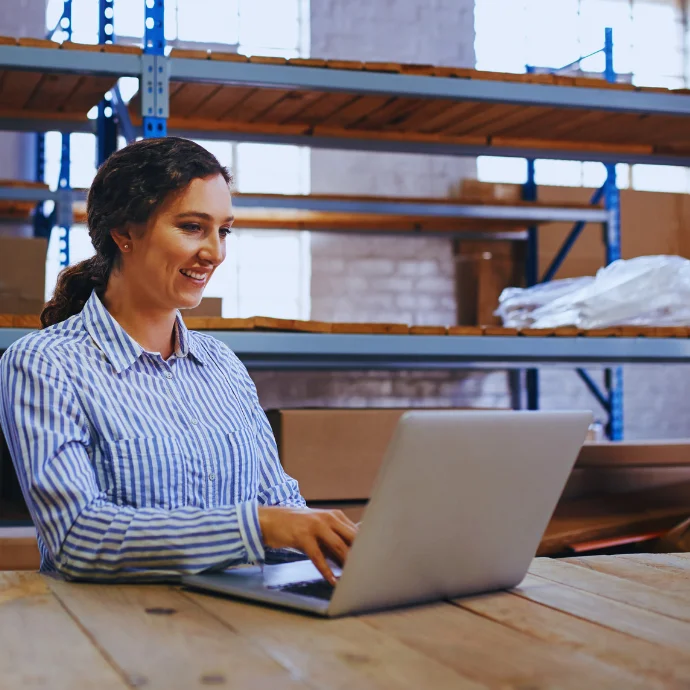
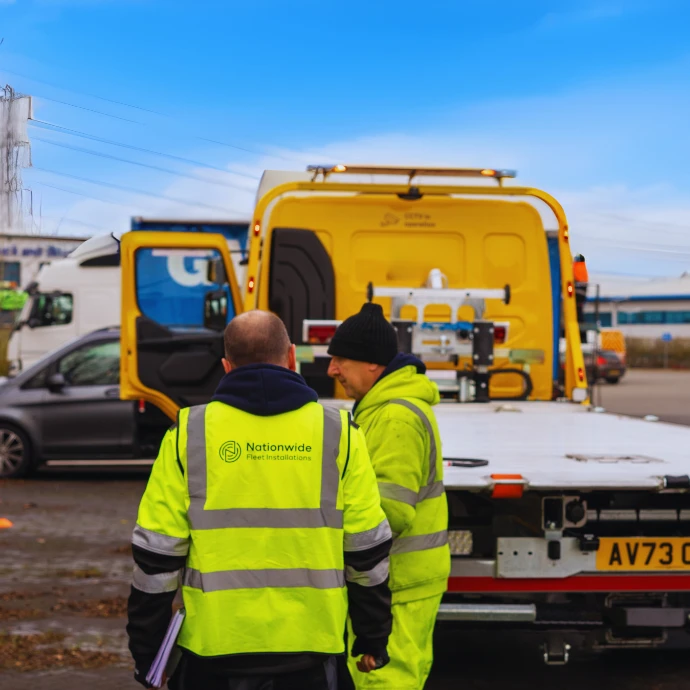
Stakeholder Requirements
The process begins with the Project Manager liaising with all the stakeholders in a given project. This is usually the equipment supplier and the end customer, though there are sometimes other providers included in the mix. The initial consultation is to determine key factors that will affect the rollout of installations, notably the rate of supply of the vehicle technology itself and the availability of the fleet for installation.
Health and Safety
The safety of our installation engineers is our top priority, so part of the project management discussions will be to ensure that they have a safe environment in which to work, are permitted regularly scheduled breaks, and that their mental health and well-being are taken into consideration.
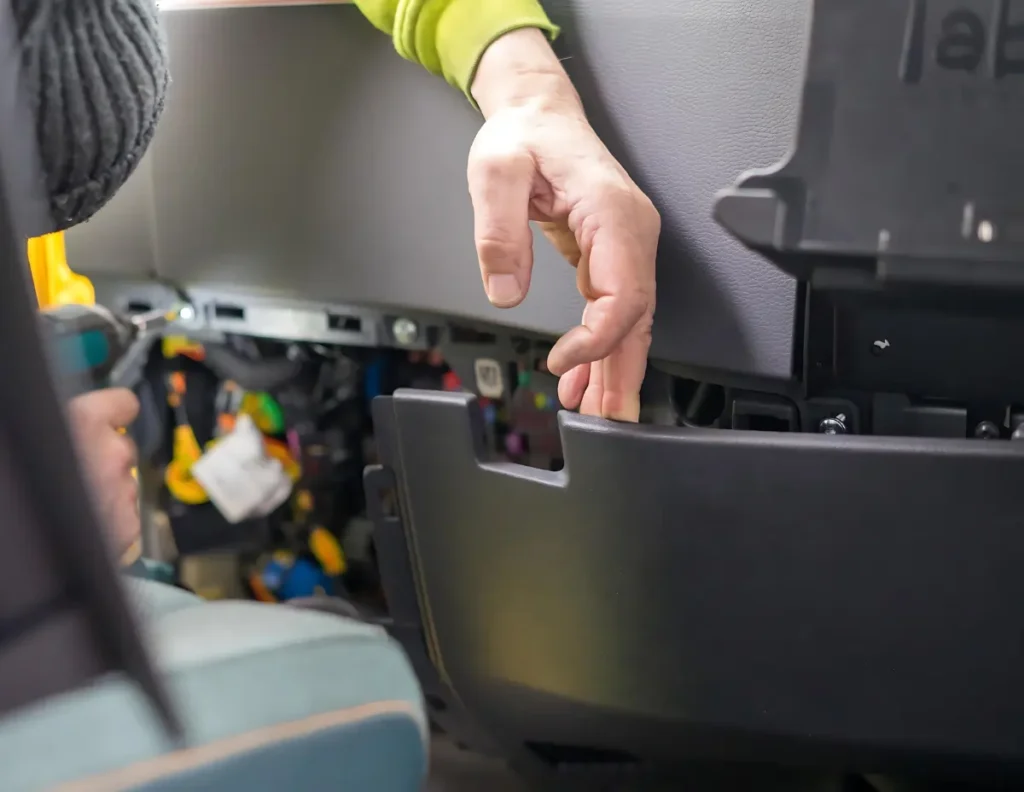
Rollout & Resource Allocation
Once the above factors have been resolved, we can develop a suitable project rollout plan and allocate our engineering resources accordingly. At this phase of the operation, the project is handed over to the Project Support Team, which deals with administration and planning as well as the physical handling of stock.
Stock Handling
Incoming stock will be checked to ensure that what is received is what was expected and to log any discrepancies in the final figures. Taking the time to log all inbound equipment at this early stage is crucial for avoiding losses later down the line. Only by knowing exactly how many units we have received can we guarantee a full installation process for your fleet. We don’t want to get to the last few dozen vehicles and realise that not only are there devices missing, but we have no idea if we even received them.
Controlling Stock and Installation
As part of our stock handling process, we electronically scan all serialised equipment to produce a detailed and accurate equipment list that we pass onto our administration and planning teams. This gives them tighter control over equipment deliveries and the associated equipment information required by each site or installer. This helps us to resolve any discrepancies in equipment information that might occur during the installation phase and maintain our record of 100% data accuracy.
Fleet Data
As well as logging all inbound equipment, our Project Support Team will also compile a list of fleet vehicles requiring installation. This information will be supplied by the end user and will include full fleet data, including VIN, vehicle registration number, fleet number, depot or base location, and any other pertinent details. By pairing the fleet information with the equipment data, we are able to resolve any discrepancies between the two as quickly as possible.
Get In Touch
For expert project management for any size of fleet installation project across the UK, contact Nationwide Fleet Installations today.
Call us on 0161 786 6600 or email the team at info@nationwidefleetinstallations.com, and one of our team members will get back to you.